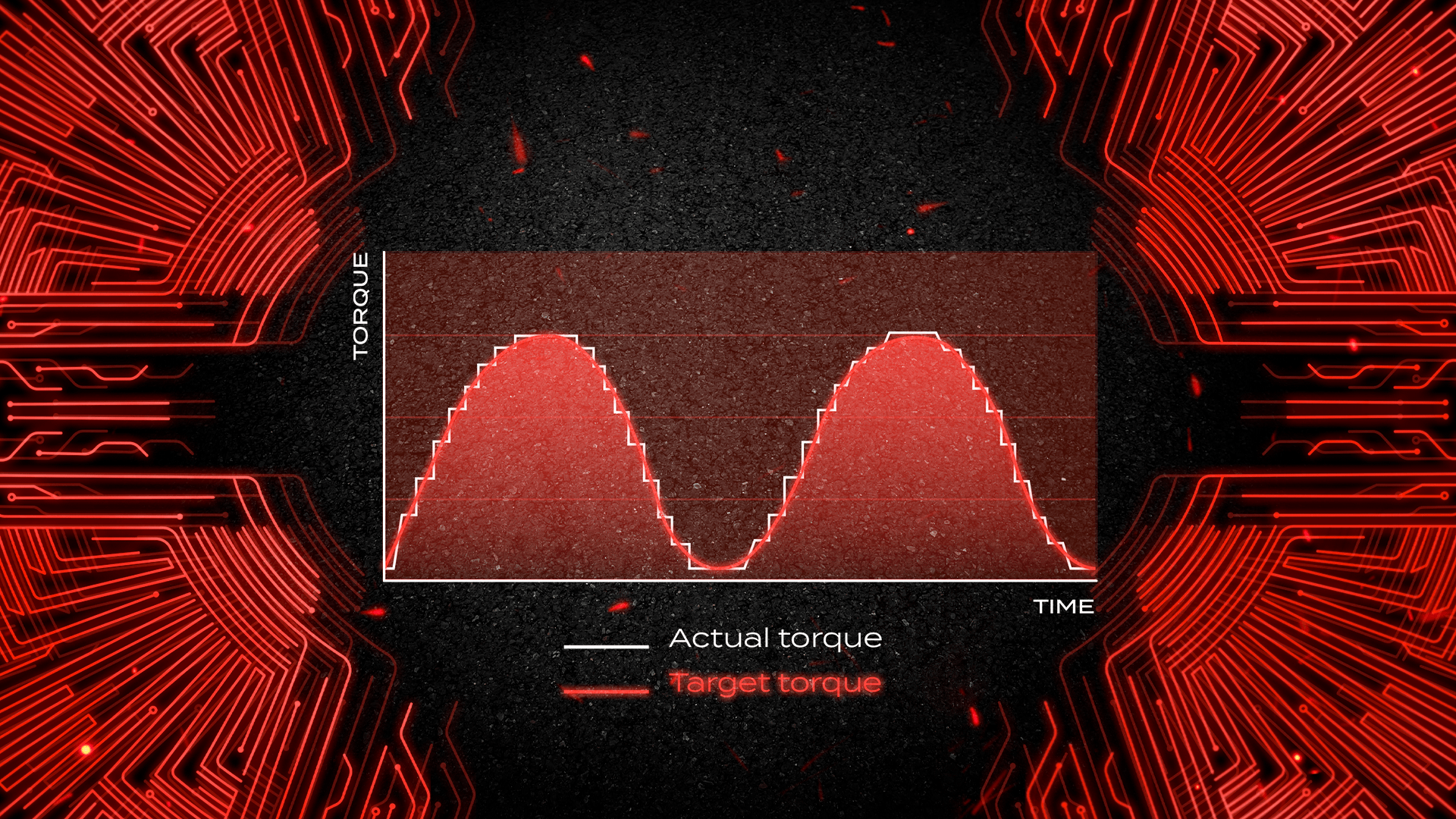
Everything you need to know about cogging: Definition and consequences
Every year, sim racing reinvents itself and revolutionizes the way motorsport fans experience their passion through a screen. Thanks to increasingly advanced technologies, the gap between the real and the virtual is rapidly diminishing.
Despite these great innovations, some technical problems continue to persist, extending far beyond the world of sim racing and its products.
The “cogging torque” of a motor, more commonly referred to as “cogging”, is one such phenomenon that leads to technical complications. It significantly impacts racing, with variations in speed depending on the position of your wheel rim. Knowing what causes this will help you better understand your configurations and setups while fully grasping the technical aspects of this type of external effect on your products. All these explanations will ultimately provide a way to reduce cogging in your games.
What is “Cogging torque”?
Cogging is defined by several elements. This phenomenon, which is not specific to the world of sim racing, is a physical result well known to engineers.
This undesirable element of a motor is the result of the interaction between the magnets positioned on the rotor (the rotating part of the machine) and the coils positioned on the stator (the part generating the rotating magnetic field) of the motor. Each time a pole passes (meaning a magnet passing in front of the coil), it will generate a non-linear electromagnetic current, giving rise to periodic resistance points (resisting torque) due to the switch from one magnet to another.
Cogging then becomes an element which hinders the low-speed operation of the motor, by generating torque ripples and positioning errors between the wheel rim and the simulation. The major consequence is variations in speed, depending on the position. For the sim racer, the feeling is different, with a type of resistance or jerk that is felt when turning the wheel rim in a sim racing game, which can make the steering jerky rather than smooth.
In the case of sim racing, cogging torque will impact products featuring Direct Drive technology. Why? Because Direct Drive products are equipped with this same electromagnetic technology, including a rotor, a stator, magnets, and so on. Just to be clear: this is the same technology that’s used in washing machines, meaning that cogging isn’t a problem exclusively related to racing simulation.
(This excludes all racing wheel bases that use gears, which have a more limited lifespan and provide a less realistic racing feel.)
The reasons for this type of phenomenon
There are many reasons for cogging! They can also generate more or less effects. Here are some examples:
- The number of poles: The greater the number of magnets, the more quickly the magnetic field will vary over a given rotational distance.
- The strength of the magnets: More powerful magnets increase the strength of the magnetic field, which can increase variations in cogging torque. The forces of attraction and repulsion between the rotor magnets and the stator teeth become more pronounced.
- The design of the ferrite core: The ferrite core guides and concentrates the magnetic field produced by the magnets. A ferrite core with good magnetic conductivity can concentrate the magnetic flux in specific areas. This concentration can create local variations in the magnetic field, which manifest themselves as a cogging effect.
- The thickness of the stator coils: A thicker coil can generate a more intense magnetic field. This increased intensity will accentuate local variations in the magnetic field when the rotor turns.
The consequences of cogging
It is certain that a racing wheel base suffering from “cogging” will be more difficult to control. The gap between the game’s simulation and the motor will have to be compensated for by a computer system. At each pole crossing, the software must adjust the force applied to compensate for the “cogging” torque.
The “waves” perceptible through the sensors, which are used to control the motor, will be picked up and integrated directly into the steering calculations. Then you know what happens next: bounces and jerks that make it difficult to perfectly control the position.
3 major consequences:
- Oscillations (Problems with control)
- Jerks (Loss of realism)
- Permanent vibrations not intended by the game (Fatigue)
It goes without saying that this phenomenon is detrimental in the context of sim racing, which requires using the motors at very low speeds, or even at a standstill.
How to resolve cogging issues on a sim racing base?
The “anti-cogging” algorithm
Some racing simulation software incorporates algorithms to compensate for cogging torque. These algorithms analyze the behavior of the wheel and adjust the forces accordingly, to provide a smoother and more natural feel. This is one of the most common methods in sim racing — to be used only if the motor itself cannot arrive at a solution through its materials or design.
The main advantage of this solution is that it is very inexpensive, but it does have certain disadvantages:
- Reduction of ripples and jerks by the filter, but also effects coming from the game.
- Torque reduction to compensate for torque drops when changing poles.
- Use of additional processing resources.
Optimizing the topology of the motor
Manufacturers can reduce cogging by optimizing design and materials. As cogging is an undesirable motor effect, it’s important to treat the problem at its source! From the design stage, using more expensive materials can make a big difference: for example, using higher-quality copper windings.
Why is it so important to reduce cogging torque in sim racing?
A technical phenomenon that may seem insignificant at first glance in a highly technical discipline, in which every millisecond of a movement counts and cannot be missed, is likely to have a far greater impact than one might think.
Cogging impacts the very essence of what it means to race — a quest for pure realism that leads to the top of the podium! Reducing cogging is definitely within your reach, by carefully choosing the very best racing wheel base that will give you the performance you need!
It is this quest that drives engineers and racers to constantly look for solutions to improve their gear and, ultimately, take their racing enjoyment to the next level.